Biopuremax is a company focused on PW and WFI systems in the pharmaceutical and biotech industries.
Biopuremax has over 20 years of experience in the design, installation, validation, and operation of high-quality biopharmaceutical water systems.
Biopuremax provides a standardized package system for supplying chemical free and media free water as RO feed water.
Biopuremax’s specialty is water systems and has all in-house capabilities to design, install and commission pretreatment, purified water (PW) and water-for-injection (WFI) systems, with cutting-edge water production technologies, sanitization, reverse osmosis (RO), continuous electro de-ionization (CEDI), UF and additional new technologies for Biopharmaceutical process water treatment.
Biopuremax supplies Water for Injection systems from A’-Z’, from the conceptual design and through the detailed design, including: fabrication, programming, installation, commissioning, validation, project management and after sale services with our cutting edge technology and to the highest level of international standards.
The Biopuremax has a very compact design with a small footprint and low floor loading which reduces CAPEX and installation costs. The superb reliability combined with low maintenance drop OPEX drastically while complying with the highest regulatory standards.
Biopuremax
Testimonial Video
In pharmaceutical water treatment systems, we need to combine low life-cycle costs with the high reliability needed for PW/WFI.
The Biopuremax water system is superior to all other pharma water treatment systems as it has no chemicals and no media.
As the Biopuremax has no chemicals and no organic media, the system is guaranteed to have zero total count in the RO FEED WATER. The RO will only remove inorganic impurities as the product water will always be free of bacteria.
The only maintenance needed on the Biopuremax is replacement of the filters and of the UV lamps. The scale precipitated in the ESRTM is automatically removed by a cleaning cycle.
When the system is first started up it undergoes a heat sanitization cycle at 85°C (185°F). As heat sanitization is the golden standard for pharmaceutical systems there is no other more suitable system for pharma applications. The sanitization starts at the very beginning of the pharma water treatment system, at the city water tank. The hot water circulated through all the equipment and piping in the system up to the product water storage tank.
The Biopuremax system operates continuously and reduces bacteria because of the Electrolytic Scale Reducer (ESRTM) and Hydro Optic Dechlorination (HODTM). The ESRTM generates free chlorine from the naturally occurring feed water chloride and will reduce total microbial load. The Hydro Optical Dechlorination (HODTM) will also very effectively disinfect the water as a byproduct of the dechlorination process. Heat sanitization is needed only at startup and after maintenance, as the bacteria are continuously eradicated during operation, so the Biopuremax can easily be validated.
The constant reduction of bacteria due to system operation is called: Continuous Bacterial Reduction or CBR.
For WFI the Biopuremax system is the best choice as the low systemic bacteria high reliability and absence of chemicals make it uniquely compatible for pharmaceutical water for injection systems.
Pharmaceutical plants usually struggle with the question “what is the right pharmaceutical water treatment for us and also how to choose the right pharmaceutical water system design for reliable operation and easy validation”.
Biopuremax is the house for all those services and supplies pharmaceutical water systems from A’-Z’, starting from the conceptual design and all the way through the detailed design, fabrication, programming, installation, commissioning, validation, project management and after sales services with cutting edge technology to the highest level of international standards.
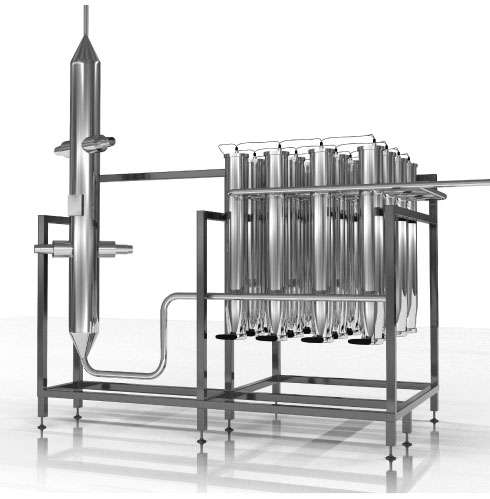